Quality - The Secret Weapon to Accelerate Time-to-Market in Medtech
Jul 06, 2022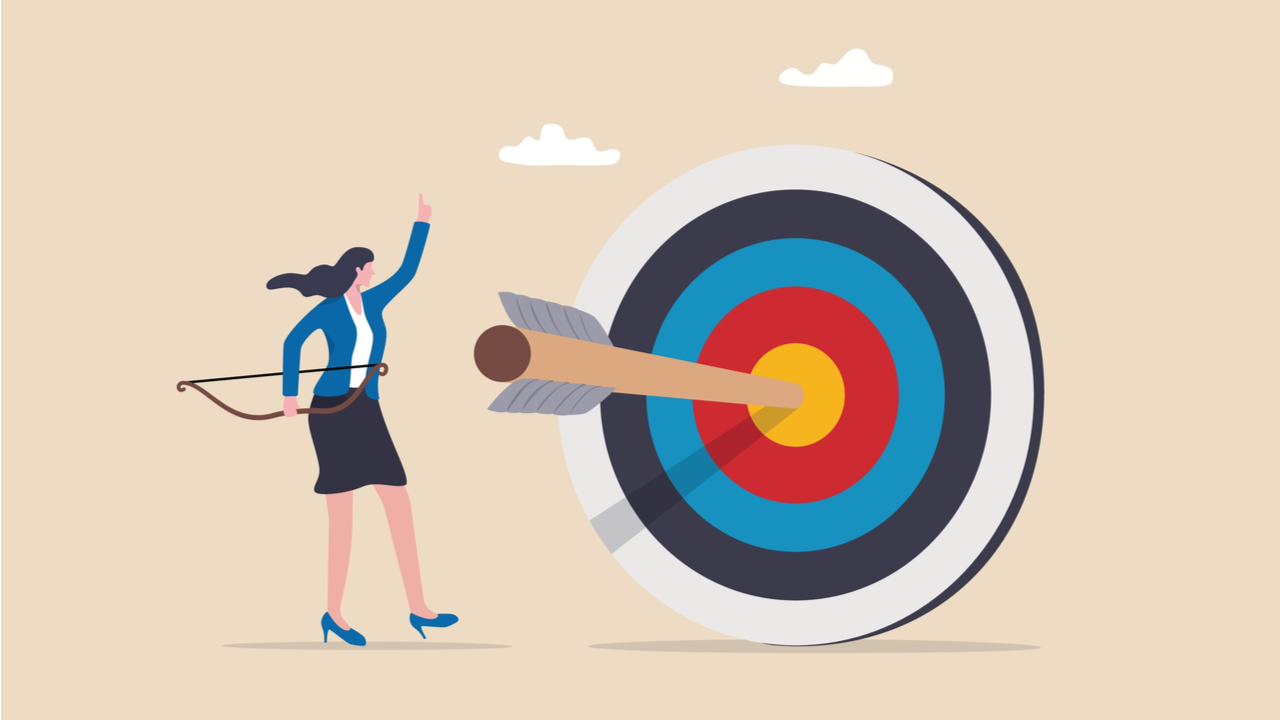
Most of the time, quality (as in “quality management”) is only considered after a design concept is mature, if not finalized. Design control, document control, risk management – they are considered checkbox activities that are simply needed for regulatory purposes. Unfortunately, this is the way that the majority of medtech startups operate, which destroys development timelines and budgets by way of massive redo loops.
Instead, companies should think of quality as a sword (not a shield). Quality management should be proactively deployed to help teams not only prepare for regulatory submission but more importantly ensure that the right product is being developed and the right processes are efficiently making it happen.
Here are 5 ways that Quality can be used as a weapon to accelerate time to market in medtech:
1. Use Quality to Align Teams
Ever been part of a team where requirements weren’t written down, roles and responsibilities weren’t clear, and critical processes were trapped in a single person’s head? Lack of clarity creates confusion, confusion creates rework, and rework creates delays.
Proactive quality gets teams on the same page, which creates the right focus, and results in accelerated timelines. Here are a few quality documents that help teams align:
- User Needs – It sounds so simple and obvious. Write down the intended benefits and constraints to users and customers. Then, use these documents to define the right solutions. Having a solid set of user needs aligns a project team on a common set of goals and accelerates progress.
- Design Inputs – Translating User Needs into Design Inputs that characterize the device is a critical yet often deferred activity. Usually, startup teams believe that design inputs will fall out of the first iteration or MVP. While it may not be practical to define every design input out of the gate, create a baseline version to communicate the knowns. This will improve clarity and reduce development time.
- Design & Development Plan – Who’s doing what? When roles and responsibilities are in question, it is difficult for teams to operate efficiently. Use a Design and Development Plan to clearly indicate the key players and their responsibilities throughout development. This will improve communication, reduce confusion, and accelerate timeline.
- Process Flow Charts - What is the product development process? Where are we now? What comes next? A simple flow chart can be extremely useful tool to communicate the product development steps and their sequence. Create a product development flow chart, put it up on a wall and/or intranet, and reference it when questions surface around the development process. Your team will gain alignment around the process, which will speed things up.
2. Use Quality to Identify and Focus on the Right Risks
Most teams put-off risk management until the functional device design is mature. Risk management is often viewed as a checkbox activity, thinking of it primarily as a documentation exercise.
But reactive risk management can wreak havoc on a schedule. When risks are discovered late in the game, it can cause massive design overhauls and redo loops. These redo loops could have been avoided through proactive quality and risk management.
One of the first steps that teams should do in risk management, long before diving deep into risk analyses and mitigation strategies, is defining the hazards. Hazards are the potential sources of harm to a patient that could be caused by a device.
Hazards could include the following:
- Chemical hazards
- Electric energy
- Mechanical energy
- Electromagnetic radiation
- Thermal hazard
- Biological hazards
- Hazards through (false) information such as manuals or advertisements.
But hazards should also be considered from a business context. What are the sources of harm to the business? These could include the following:
- Existing intellectual property (prior art)
- Costs of development and manufacturing
- Customer willingness to pay
- Legal liabilities
- Future Investment
Thinking through hazards – both clinical and business -- at the front end of development triggers new user needs and design inputs. This forces the team to be honest about the goals AND the constraints. When a team has a comprehensive look at the factors that need to be considered in developing the device and growing the business, it focuses efforts on the right activities and reduces the potential for massive, expensive redo loops.
3. Use Quality to Optimize Onboarding and Training
Have you experienced the frustration of joining a company and a year later still not knowing how basic procedures are done? If so, you’re not alone.
Onboarding and training team members on how things are done rarely goes as well as it could. When your teammates aren’t properly trained, they will conduct activities in a way that differs from your best practices. This in turn results in rework, which slows down development.
So, take the time to train. Training is a critical component of any quality management system and just good business practice. Specify the right procedures that need to be reviewed, understood, and applied by each team member. Create a training log to have employees sign-off on their training. Implement quizzes to ensure that the training has been effective.
A way that many companies are streamlining training is through video modules. Creating a library of videos that capture critical processes and showcase examples can be a much more effective way to learn than reading a standard operating procedure (SOP).
4. Use Quality to Prevent Redundant Data
If you want to see an engineer flip his lid, tell him that the model he has been developing over the last week is redundant and conflicting with a model that has been developed by another engineer. Overwriting data is a common and frustrating experience that results in massive rework after realized.
Part of quality management is document control. Good document control ensures that the right data storage repositories are created, check in/out functionality is in-place, and approvals are conducted for critical records, such as requirements documentation, drawings, specifications, protocols, etc.
Get a document control procedure in-place to specify where data is housed, how revisions are applied, and how records are approved. Implement product data management (PDM) software solutions for technical data that is routinely shared by multiple people. Taking these steps will reduce training time, frustration, and development rework.
5. Use Quality to Avoid Engaging the Wrong Vendors
Have you ever realized too late in the game that a vendor selected for a particular process wasn’t really qualified to do the work?
A critical part of quality management is ensuring that the vendors selected are properly qualified to perform their contracted activities. When starting a new relationship with a vendor, teams want to get off on the right foot. So, questions about quality systems, certifications, and the like may be put on the back burner. This is often a mistake.
Any vendor that you engage from a development firm to a contract manufacturer should be audited at the front end to ensure that they are an adequate partner to fulfill the needs of your business. This generally starts with an audit form that vendors fill-out with their quality details.
Certifications are also a good filter to determine some qualifications. For instance, there are many companies that claim to be “ISO 13485 compliant”. But, there is a huge difference between self-labeled “compliance” and “ISO 13485 certification”. Certifications require external audits by notified bodies to confirm that the right procedures are in-place and being followed. In the medical device business, it is a far safer route to pursue engagements with companies that are ISO 13485 certified.
Engaging the wrong firm can be a major time sink. Not only can it be extremely difficult to capture all work product when you need to make a change, but it can result in a significant amount of time (and cost) wasted getting a new, more qualified firm up-to-speed.
Summary
Most companies operate quality management in a reactive mode. They think of it as a checkbox activity, or “the tax” a company needs to pay to be in the medical device industry. This is a missed opportunity. Quality has the potential to align teams, focus on the right risks, optimize training, avoid data redundancies, establish the right partnerships, and more. Used proactively, quality is a powerful weapon to accelerate development timelines while ensuring regulatory compliance.
Archimedic has a program that bundles our ISO 13485 QMS with a part-time quality expert to help you rapidly implement and maintain proactive quality at your company. Interested in learning more? Check out the link below.
Join the conversation
Drop your email below to receive these articles delivered to your Inbox as soon as they're published.Ā